Distributed intelligence makes flow of goods fit for the future
by JENS KAROLYI on Sep 3, 2024 10:00:00 AM
Two Rolling On Interroll (ROI) partners have implemented a seamless material flow solution at a US distribution center operated by Arvato, one of the world‘s leading contract logistics providers. The project, consisting of highperformance conveyor and sorting systems with intelligent control and seamless integration of labeling robots, shows how increasingly demanding material-handling requirements can be flexibly met and future-proofed.
With nearly 100 locations and 17,000 employees around the globe, Arvato is one of the world’s leading contract logistics companies. The company operates nine facilities with about 430,000 square meters (4.6 million square feet) of storage and office space in the US alone. Its state-of-the-art distribution center in Shepherdsville, Kentucky, accounts for almost a quarter of this, at 90,000 square meters. The gigantic facility is used to store approximately 80,000 pallets and 10,000 different items belonging to two electronics suppliers, with their products delivered on a continuous basis to both companies and consumers. To streamline operations, Arvato commissioned the ROI partner EQ SOLUTIONS, a complete supplier of state-of-the-art storage and automation solutions and long-term collaborator of Arvato, to automate material-handling processes and provide subsequent maintenance services. The goal was a throughput of 3,600 pieces conveyed per hour. To help achieve this complex task, the material-handling design company AuthenTEK Solutions of Texas, and Interroll, with its modular platform solutions, were selected as partners. The result is a prime example of a strategic cooperation where ROI partners effectively complement each other’s expertise.
Keeping an eye on everything: Intuitive monitoring of the conveyor line.
Low Noise Automation
As the planned logistics processes of both of Arvato’s electronics customers were almost identical, two Interroll crossbelt sorters were used for the automatic sorting processes. Interroll’s Modular Conveyor Platform (MCP) was selected for the conveying process, which includes a line that is approximately 2.2 kilometers (1.4 miles) long. Both solutions offer high performance, energy efficiency and long service life. They also fulfill the demands that Arvato – a long-standing user of Interroll technologies in Europe and the US – made for a system that is as quiet as possible. AuthenTEK’s robot-assisted labeling stations with multiple printers were seamlessly integrated into this conveying process. This patented solution allows different labels to be applied with great precision in and on individual cartons, for example, warning labels. This eliminates the risk of missorting, which leads to delayed shipments.
Simplified Functionality With Decentralized Controllers
However, the highlight of the Shepherdsville material handling solution is the intelligent control concept of the zero-pressureaccumulation conveyor system. This involves a decentralized machine control system, which Interroll’s multi-protocol-capable MultiControl controllers offer as standard as part of the MCP. It enables, for example, the sensors and the RollerDrive to be integrated directly into the fieldbus level. As a result, there is no need for an additional sensor/actuator level with extra gateways. Furthermore, the MultiControl’s intelligent conveying logic simplifies the design of a zero-pressure-accumulation conveyor based on a programmable logic controller (PLC). This reduces the resulting data traffic because only key decision points in the system need to be accessed at PLC level. The overall system can also be visualized on screens.
Seamless integration: Robot-assisted labeling station in the flow of goods.
No More Control Cabinets
Thanks to the AuthenTEK solution, the usual on-site PLC in the control cabinet is replaced by a PLC function in the cloud. This approach offers several advantages. First, there is no need for fixed, hardwired control cabinets, which make subsequent system redesigns more difficult and significantly reduce the flexibility of this automation solution. Second, the operation of the conveyor can be monitored online in real time. In addition to the machine control system, the decentralization concept also applies to the conveyor system’s power supply. Instead of supplying the entire conveyor via a central connection in the building, there are decentralized power supplies. This means that there is no complex cabling here either, reducing the number of possible error sources. The overall result is a pioneering design that takes the idea of smart decentralization to its logical conclusion.
Decentralized intelligence: MultiControl built into the Modular Conveyor Platform (MCP).
INTERROLL MULTICONTROL
A Simple Step Toward A Networked World
The MultiControl is used to control decentrally driven conveyor lines, ensuring zero-pressure accumulation in the flow of goods. It can also be integrated with the industry’s most widely used standard protocols (PROFIBUS, EtherNet/IP and EtherCAT), future-proofing communication connections.
In addition to autonomous conveyors without PLC, MultiControl can be used to create real-time solutions with a PLC. Thanks to the use of open and standardized protocols, the system status can be monitored in real time – a basic requirement for smart material handling systems. It is also possible to select between different process images, so that, depending on requirements, a system integrator can implement an optimal solution taking the variety of data read out and the desired PLC capacity into account.
Read inspiring success stories and discover how Interroll's solutions helped businesses maximise their operations!
Curious how Interroll's Modular Conveyor Platform can improve your material flow?
You May Also Like
These Related Stories
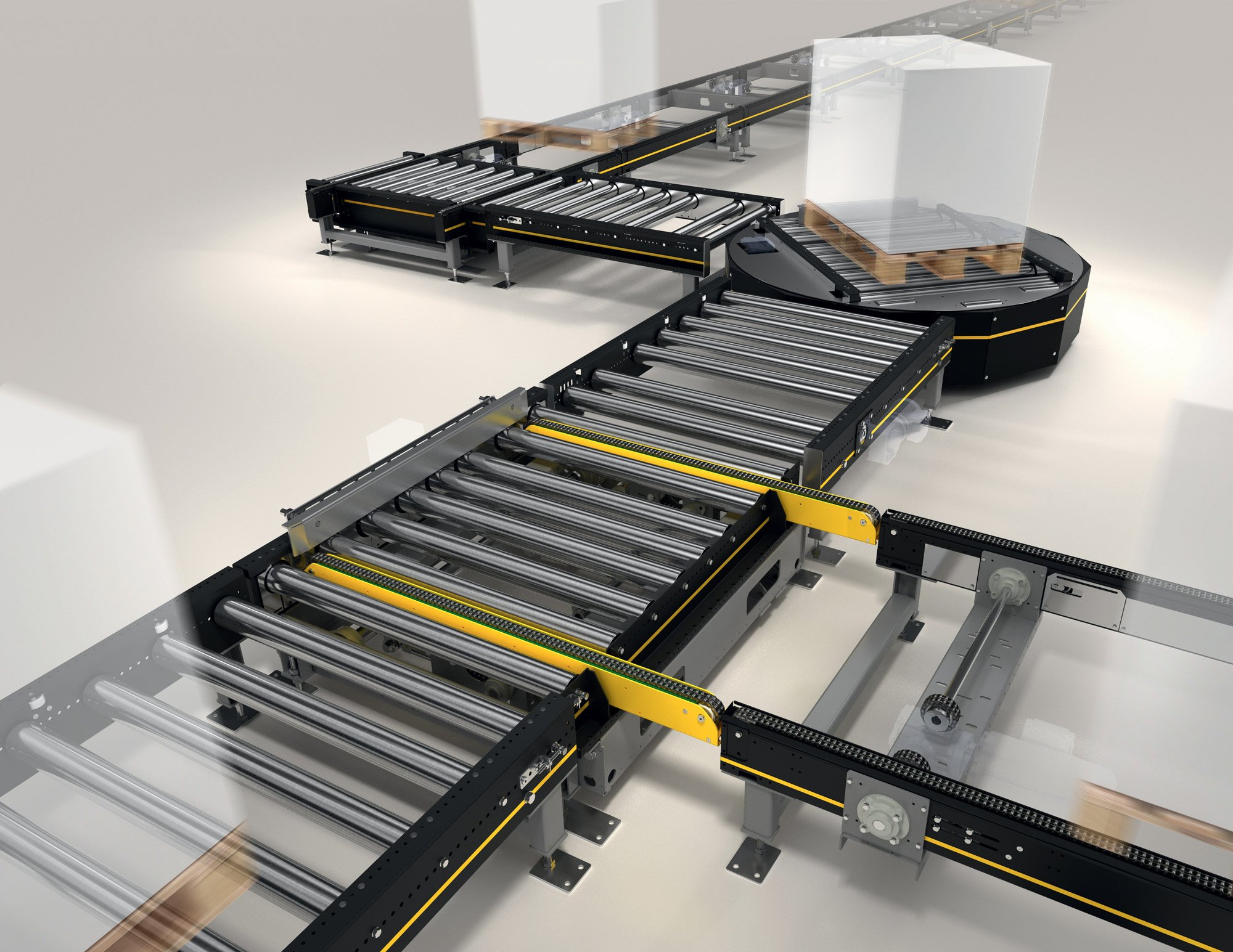
A seamless solution
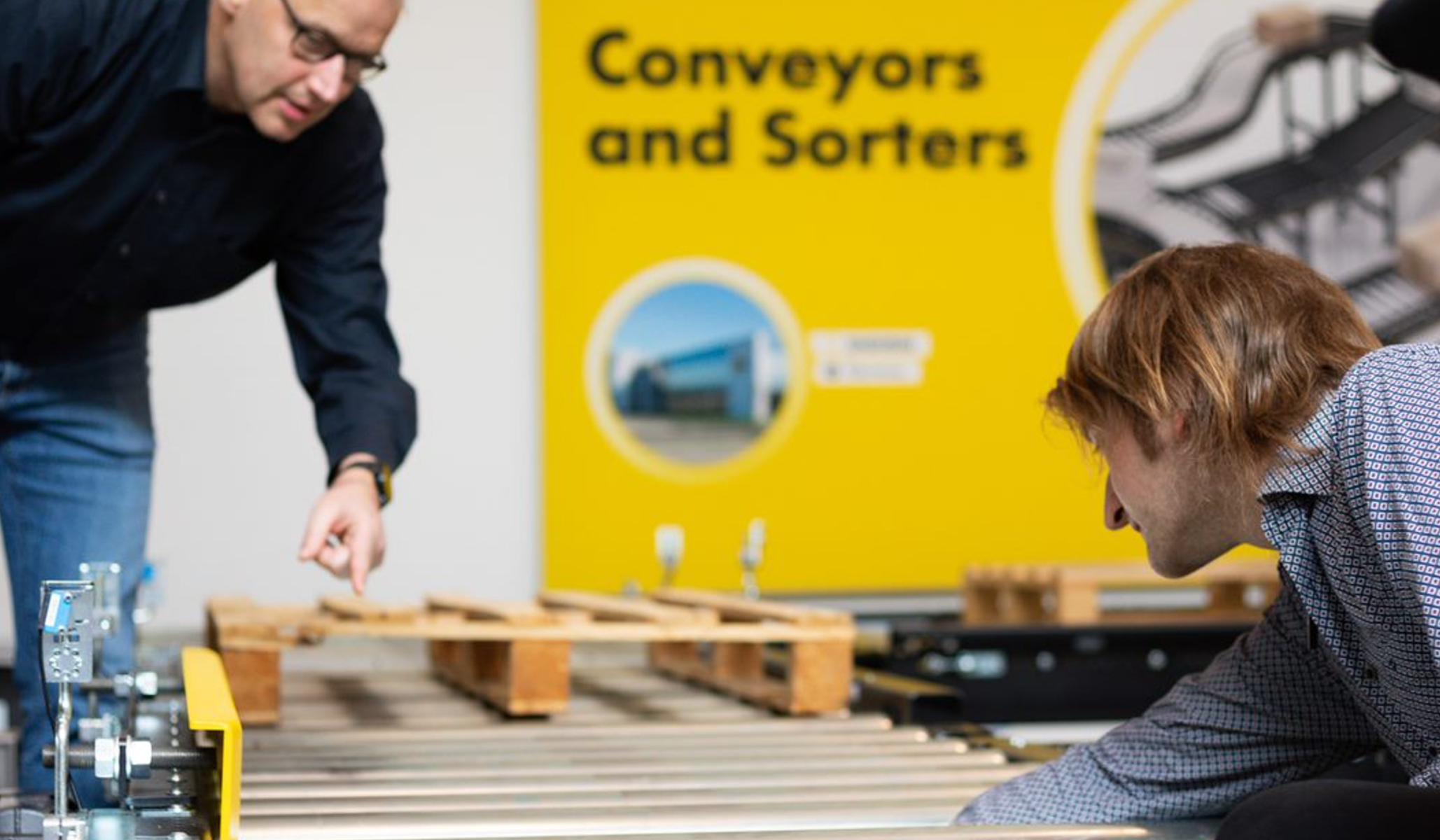
Increase safety and reduce cost with automated Pallet Conveyor Systems
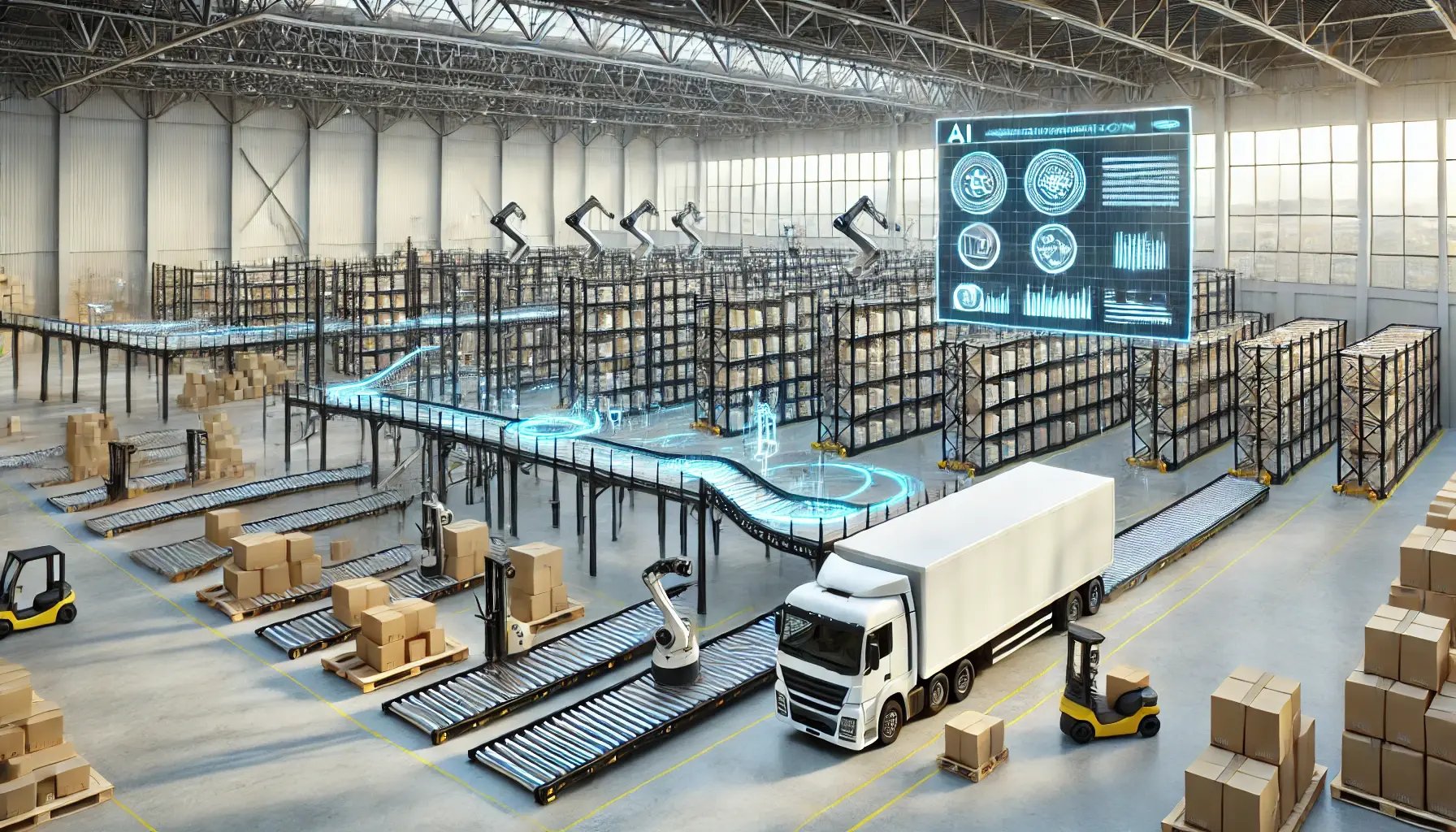