A seamless solution
by HANS-PETER OTT on Jul 26, 2024 10:15:00 AM
A combined retrofit and expansion project at a distribution center of Rossmann – one of Europe’s largest drugstore chains with over 4,500 outlets – shows how performance and energy efficiency can be improved within existing warehouses. The recipe for success? The seamless interaction between Interroll’s Modular Pallet Conveyor Platform (MPP) and Modular Conveyor Platform (MCP) as well as between project partners.
Most people don’t give much thought to the process of buying a bottle of shampoo or a toothbrush. Head to the drugstore, choose a product, leave. Easy. Yet many customers would be amazed by the process that helps get products on the shelf in the first place. The drugstore chain Rossmann operates 2,200 stores in Germany, each offering a range of over 18,000 products. To ensure it can flexibly, quickly and sustainably supply its outlets, the retailer runs a sophisticated network of ultramodern distribution centers. A key component of this logistics operation is a central warehouse near Leipzig. Around 1,100 employees work in the facility, home to a high-rack and smallparts warehouse as well as a number of retrofitting and picking functions. The combined effect is a seamless journey of goods from arrival to issue. Automated pallet and container conveyors are used in the process of depalletizing incoming pallets into containers, moving the containers to temporary storage and palletizing them again for shipping.
New Systems For Pallets And Containers
But Rossmann, a long-established family business, recognizes that continuous modernization of its automated material-handling processes is key to the warehouse’s success. Systems integrator BSS Bohnenberg was commissioned with replacing sections of the existing conveyor system, setting up additional workstations to retrofit the pallets into containers and automate the palletization of storage containers. Interroll and Rolling On Interroll (ROI) partner Schwingshandl were chosen as partners to handle this task. The seamless combination of expertise and technologies ensured that the new solutions could be installed during operation.
A Combined Conveyor Platform
The workstation expansion carried out involved extending the capacity of the goods-in unpicking area. Here, bulk pallets are unpacked and sorted into smaller, more manageable containers for storage and, later, commissioning. Eight new manual workstations were added, combining Interroll’s Modular Pallet Conveyor Platform (MPP, used for heavy goods) and Modular Conveyor Platform (MCP, used for lighter goods). The MPP pallet conveyor is used to feed the bulk, single-product pallets to each workstation. After unpicking, empty pallets are then returned automatically with zero pressure accumulation via an MCP that is driven by Interroll’s 24-volt RollerDrive. This precise and highly versatile conveying process avoids possible malfunctions that would otherwise have to be resolved manually. An MCP conveyor is also used to feed the empty containers and transport filled containers from workstations to the storage area.
Integrated And Automated Palletizing
The second task involved integrating an automatic loading and palletizing machine from Schwingshandl into the combined MCP and MPP conveyor platforms. It was centered on a specific area of the warehouse that handles especially sensitive products. Here, an MCP conveyor feeds already picked storage containers to the machine, which automatically stacks several of them onto a single pallet. Loaded pallets are then transported onward via the MPP pallet conveyor toward goods issue.
Retrofitting Offers Significant Energy Efficiencies
A conveyor retrofit made up an additional task. Some of Rossmann’s existing conveyors had become worn and needed replacing. Older sections were therefore replaced by MCP modules. In addition, the conveyor system was expanded to around 900 meters (2,950 feet) in total, also using an MCP. This shows that the platform can be seamlessly integrated into legacy infrastructure and control applications. Retrofitting also achieved significant energy efficiencies in terms of cost-effectiveness and sustainability. The worn-out parts of the conveyor system at the Leipzig warehouse used a central drive concept in which 400-volt drive motors with actuators provided a flow of goods with zero pressure accumulation. However, the new, very low-noise solution built around Interroll’s MCP uses a decentralized drive concept based on the company’s 24-volt RollerDrive EC5000 and the MultiControl system, which is compatible with multiple protocols (PROFINET, EtherNet/IP, EtherCat). This can achieve energy savings of around 50 percent compared with traditional 400-volt systems, according to independent measurements. Interroll’s optional power supply units also offer significant advantages. Their high protection rating and robust housing means they do not need to be installed in a control cabinet, for example, and drastically reduce cabling and potential faults.
How Interroll's Pallet And Container Conveyors Interact
Interroll’s modular platform philosophy supports the seamless interaction between pallet and container conveying. The MPP and MCP are flexible plug-and-play systems with an integrated machine control function. They can be used in nearly all automation scenarios with zero-pressure-accumulation material handling. The MPP, for conveying pallets weighing up to 1,500 kilograms, includes robust chain and roller conveyors, as well as additional conveyor modules such as transfers and turntables. In addition to gear and drum motors, 48-volt RollerDrives can be used depending on customer needs. The globally renowned MCP is the first choice when it comes to conveying containers with conveyor weights of up to 50 kilograms, and offers impressive energy efficiency. Conveyor modules are delivered fully preassembled, minimizing installation times.
What are the challenges and trends in intralogistics in 2030? Download our trend report to learn more.
Discover how Interroll's MPP or MCP can help you excellerate your material-handling processes:
You May Also Like
These Related Stories
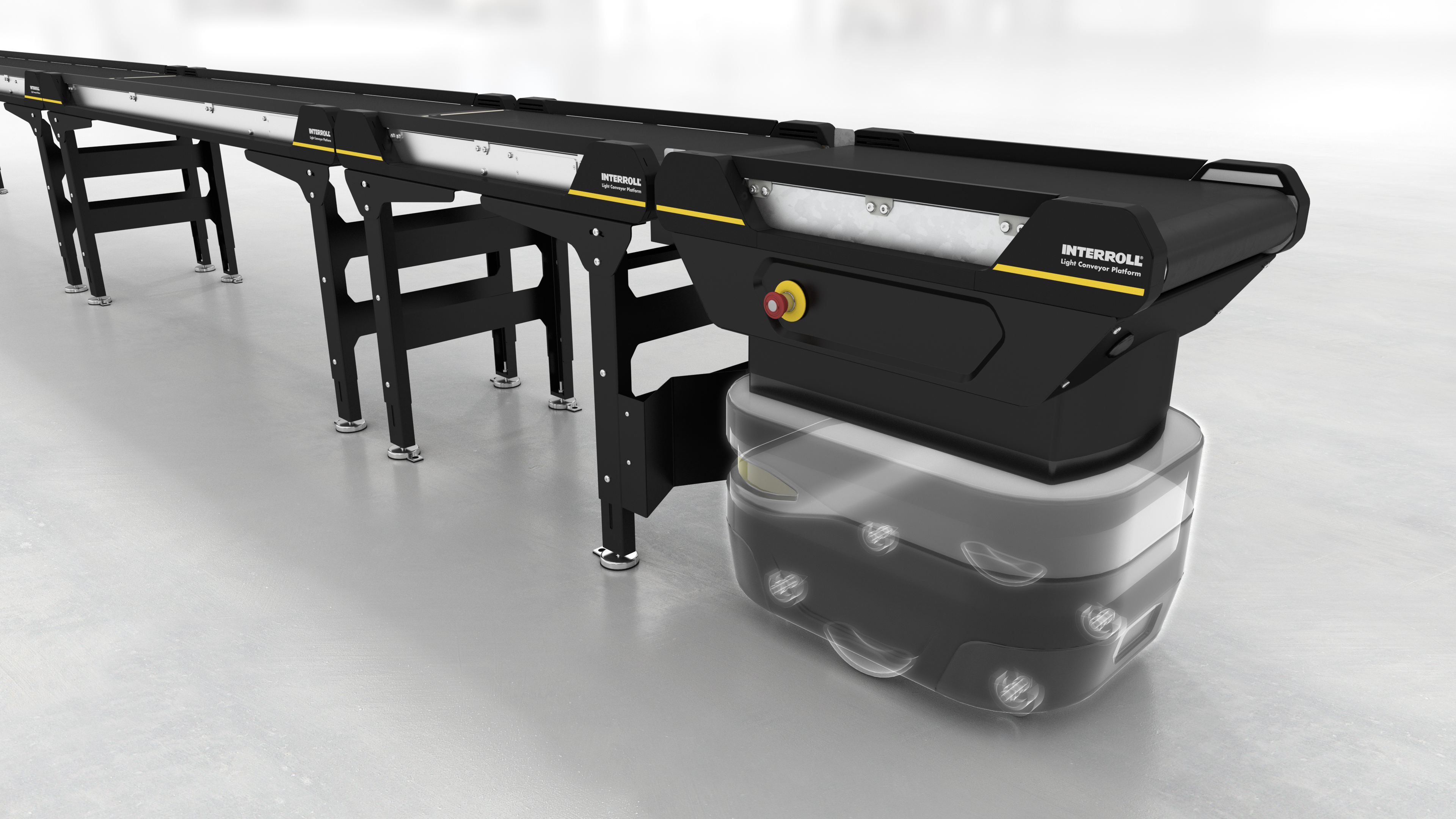
Keeping up the flow
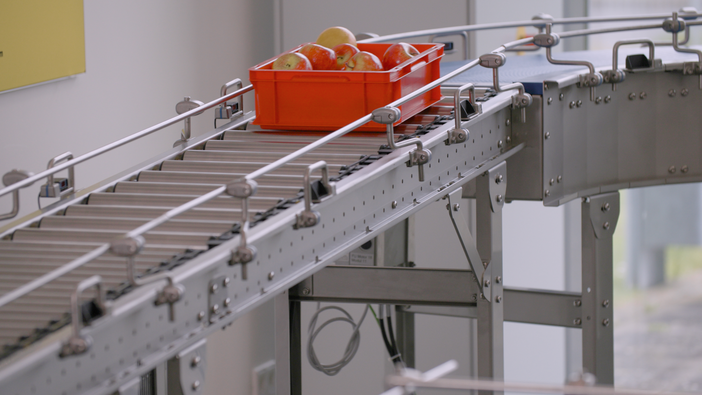
Zero Pressure Accumulation: The Biggest Benefits for Food Packaging Lines
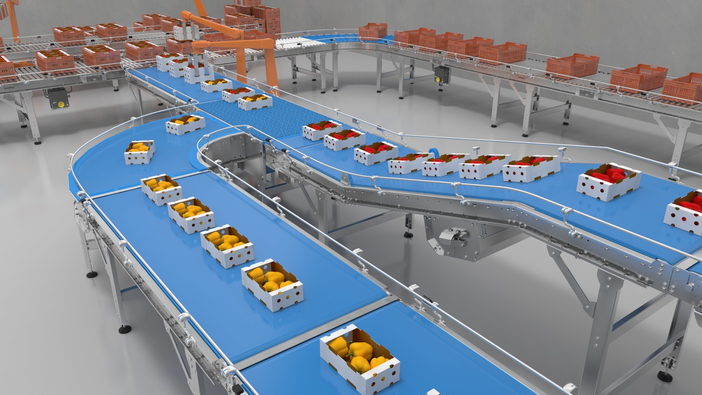