Five steps to successfully implementing a pallet handling solution
by Interroll on Dec 31, 2024 1:00:00 AM
It’s a critical moment in any project. The reasoning is watertight, the pre-implementation process is complete and roles are defined. So what now?
In the case of installing a new automated pallet-handling solution, the answer isn’t always clear. Planning, installation and operation of conveyor platforms can be a complicated and challenging process, with several parties involved, multiple options available at every stage and very tight timelines. For example, who will design and install the new system, will it fit in the space available, what’s the best way to avoid delays and who will provide maintenance after commissioning?
While every project is different, there are numerous commonalities in ensuring a successful implementation of a new automated pallet-handling solution. The purpose of this blog is to paint a picture of the process, summarize the challenges involved at each stage and outline solutions to them, with full details available in the report “Right first time: A step-by-step guide to implementing an automated pallet-handling system”.
Implementation steps: From planning to go-live
Once the pre-implementation phase has been completed, almost every installation of a new automated pallet-handling solution can be broken down into five stages: Assessment & Planning; Design & Engineering; Production & Installation; Testing & Training; and Go-live & Optimization. Each is summarized below; more detail and solution-focused information is available in the full report.
Assessment & Planning
At the beginning of the process, the end user (the customer commissioning the system) must first define their requirements. Factors to consider include dimensions of pallets, throughput requirements, available space and whether additional systems, such as scanners, will be needed.
Selecting the right product that fulfills all of the requirements and is suitable for the task is the key challenge here. Early contact with a manufacturer, such as Interroll, or a system integrator (SI; a third party contractors that specialize in installation) helps to refine customer choice and identify and address potential challenges in advance.
Design & Engineering
This stage involves defining the most suitable solution to handle the pallets. In most cases, the end user’s SI draws up the design plans, often using commercially available AutoCAD software or CAD tools provided by manufacturers. These construct a 3D model of the conveyor components.
Getting the plans right is important as errors are a major source of delays.
As plans must be signed off before production of components can begin, inaccurate designs can result in unviable components. Using a manufacturer’s own CAD software, such as Interroll’s download tool, helps to avoid such problems.
Production & Installation
The next stage is agreement of a production timeline. Lead times vary from a few weeks up to a year depending on the order. Once production is complete, in most cases end users collect components from the manufacturer’s factory. The SI will normally build and install the conveyor system.
The biggest risk at this point is installation delays. Systems may be complicated to build and require many people on site, extending build times and interfering with other operations. This increases downtimes and costs. Engaging a trusted system integrator and manufacturer with significant project management experience minimizes disruption.
Testing & Training
Once installed, the system must be thoroughly tested and staff trained in its use. System integrators are usually responsible for the testing phase, ensuring the conveyor functions correctly, meets the end user’s requirements and is safe. Training of operatives can be carried out by SIs or manufacturers.
Teething problems during commissioning are the major potential challenge. Mechanical or electrical/operational difficulties need to be quickly rectified to prevent go-live delays. Selecting proven modular systems, such as Interroll’s MPP, can help to avoid problems in the test phase altogether, or at least make them foreseeable.
Go-live & Optimization
After the system is commissioned, the SI or the manufacturer are usually contracted to maintain it. This may mean representatives of the SI or manufacturer remain on site either temporarily or permanently. Occasionally, if the end user is experienced, they may opt to undertake maintenance themselves.
A lack of long-term system reliability and comprehensive service contracts can leave end users exposed to costly downtimes once their conveyor systems are up and running. End users should, therefore, aim to strike robust long-term service agreements with SIs and/or manufacturers, such as Interroll’s Global Lifetime Service package, to ensure a fast response to aftersales issues.
What to do next
Automated pallet-handling solutions offer clear benefits over manual handling, such as improving efficiency and safety, and reducing energy usage, labor requirements and costs. But the implementation of such systems can be complex.
By addressing common pain points in advance, logistics businesses can avoid delays and smooth the path to a seamless implementation. Interroll’s extensive experience and proven pallet-handling solutions mean it is uniquely placed to achieve this. For further information, read our full implementation guide:
Getting ready and educating yourself is vital for successfully integrating a Modular Pallet Conveyor Platform. Therefor our specialist wrote a story on what you should consider. Read our implementation guide today!
You May Also Like
These Related Stories
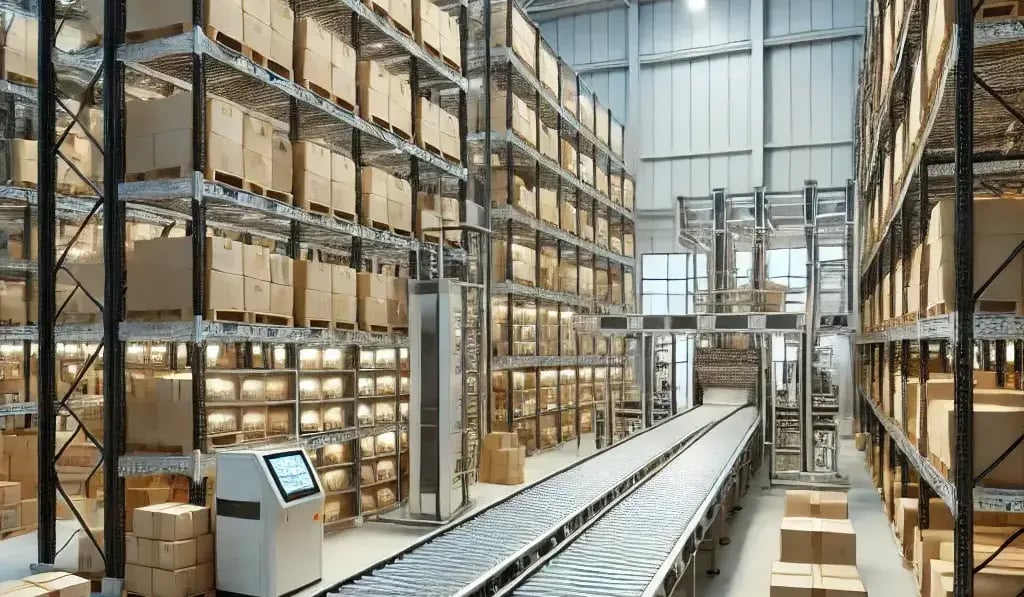
The ideal preparation for implementing a pallet conveyor system
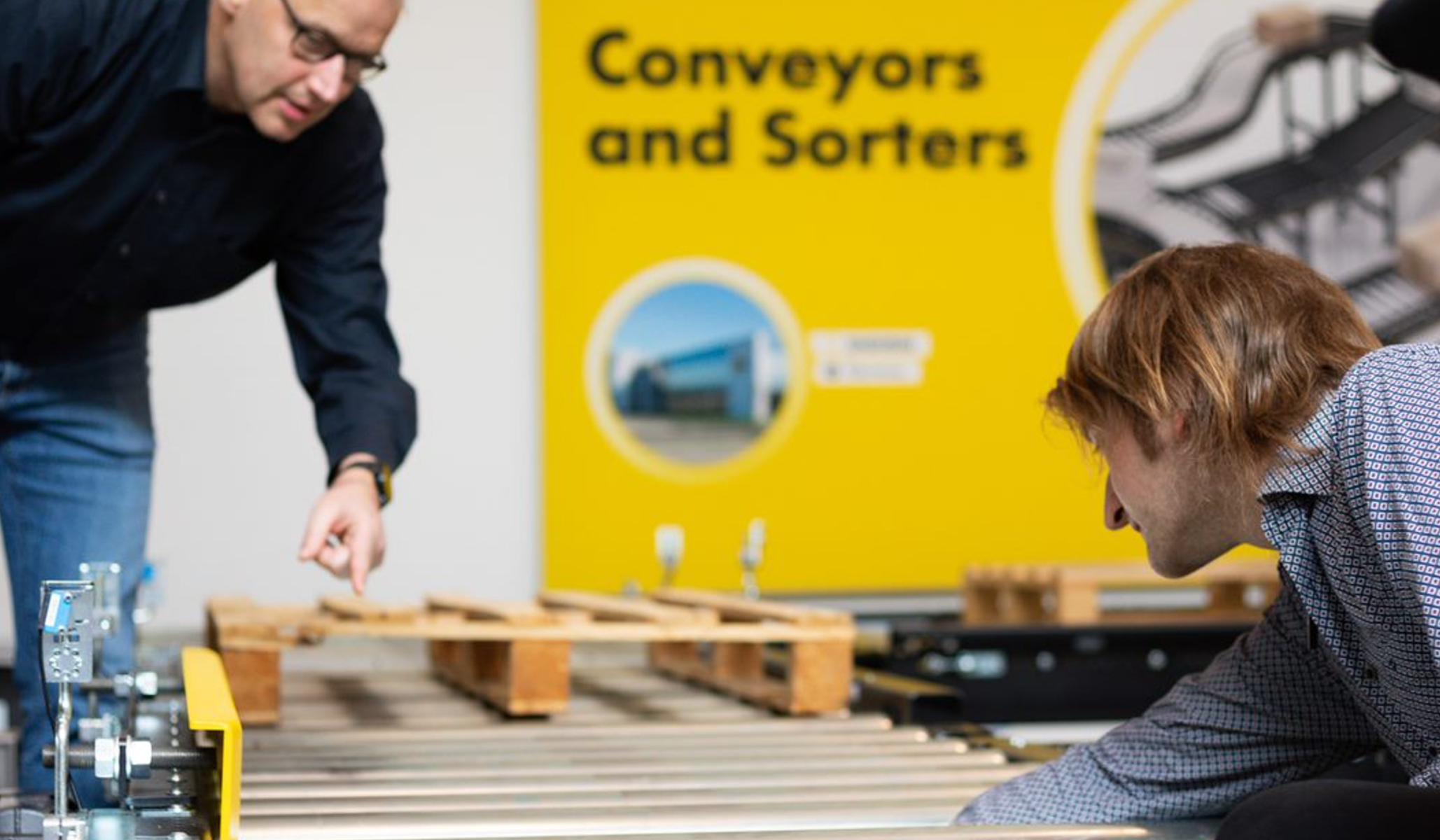
Increase safety and reduce cost with automated Pallet Conveyor Systems
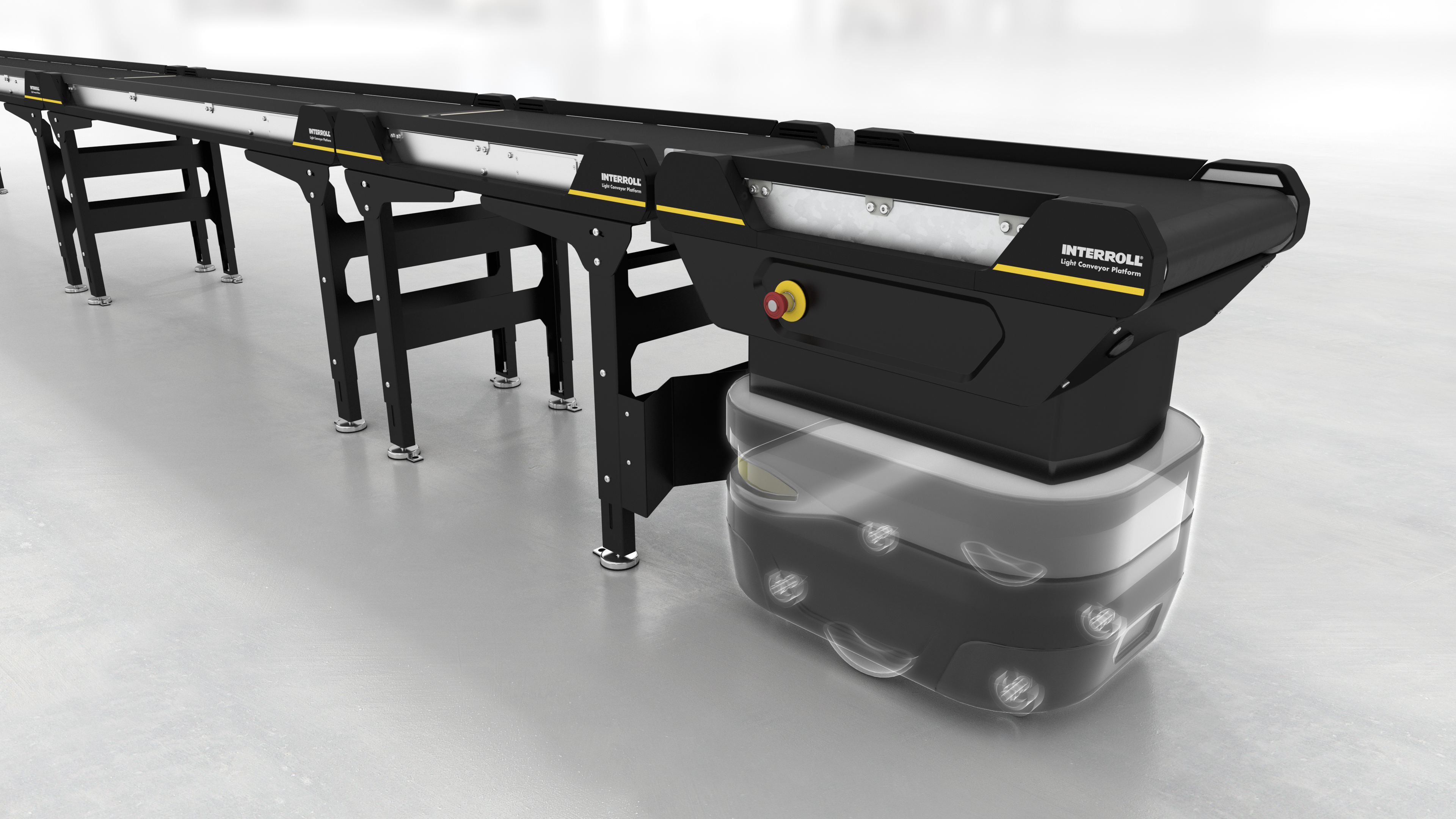