How to minimize unplanned downtime in your food packaging line
by Interroll on Jul 21, 2025 10:54:15 AM
Unplanned downtime in food packaging lines can be a significant drain on productivity and profitability. When a single component fails or an unexpected issue arises, entire production processes can come to a halt, leading to costly delays. These interruptions not only affect output but also have a ripple effect on delivery schedules and customer satisfaction. In a high-demand industry like food packaging, where margins are often thin, even minor disruptions can accumulate into substantial financial losses.
This blog explores the effective strategies to reduce unplanned maintenance and cleaning interruptions in food packaging lines through proactive measures and system design improvements.
Identifying common causes of downtime
Understanding the root causes of unplanned downtime is the first step toward minimizing it. Common causes are leaks, breakages, and contamination. A burst crate spilling liquids over the conveyor can necessitate immediate shutdown for cleaning and repairs, while breakages in machinery parts can halt operations until replacements are sourced and installed. Here are 3 tips to limit downtime to the absolute minimum:
1. Implement proactive maintenance schedules
One of the most effective strategies to minimize unplanned downtime is the setup of proactive maintenance schedules. Regular inspections and timely replacement of worn-out parts can prevent unexpected failures. By scheduling maintenance during off-peak hours, you'll ensure that your production line remains operational during critical times. Additionally, maintaining a log of past issues and repairs can help in predicting potential future problems, allowing you to address them before they cause downtime.
2. Prioritize hygienic design to prevent contamination
Effective hygienic design is crucial in preventing contamination, a common cause of unplanned downtime. This involves designing your production line to minimize areas where contaminants can accumulate and ensuring easy access for cleaning and maintenance. Focus on:- Sealed components to prevent dust and debris from entering critical areas
- Smooth, easy-to-clean surfaces to speed up sanitation.
- Accessible layouts that allow quick cleaning and maintenance.
- Intelligent control systems that only activate conveyor zones as needed, reducing wear and contamination risk.
By prioritizing hygienic design, you can prevent many of the issues that lead to unplanned downtime.
3. Evaluate and upgrade aging equipment
Old and aging equipment can be a significant source of unplanned downtime. Regularly evaluating the condition of your machinery and upgrading when necessary can save time and money in the long run. Newer equipment often comes with advanced features that make maintenance easier and less time-consuming.
When evaluating your existing equipment, consider both its age and its integration with newer systems. If a machine frequently breaks down or requires extensive maintenance, it might be time for an upgrade. Investing in modern, more reliable machinery can pay off in reduced downtime and increased overall efficiency.
By addressing these common causes of unplanned downtime, you can create a more efficient and reliable food packaging line. For more insights and detailed strategies on tackling hidden productivity killers in your food packaging line, download our new comprehensive guide.
Guide: The five hidden killers in your food production line...
and how to fix them
and how to fix them
Eliminate your productivity killers
Your line might look fine, but hidden issues could be slowing it down. This guide reveals five silent productivity killers in food packaging and how to fix them fast. Boost efficiency, safety, and output with practical insights.
You May Also Like
These Related Stories
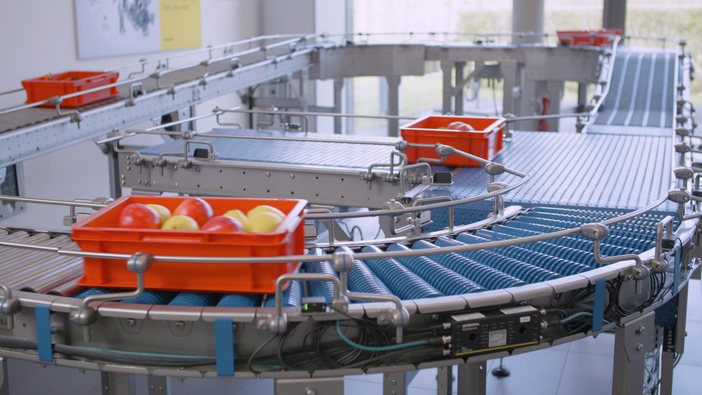
Five overlooked food production Issues that quietly disrupt your packaging process
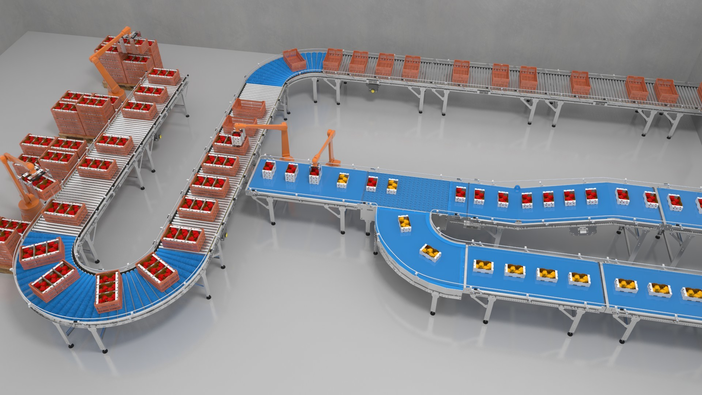
The importance of packaging integrity in food logistics
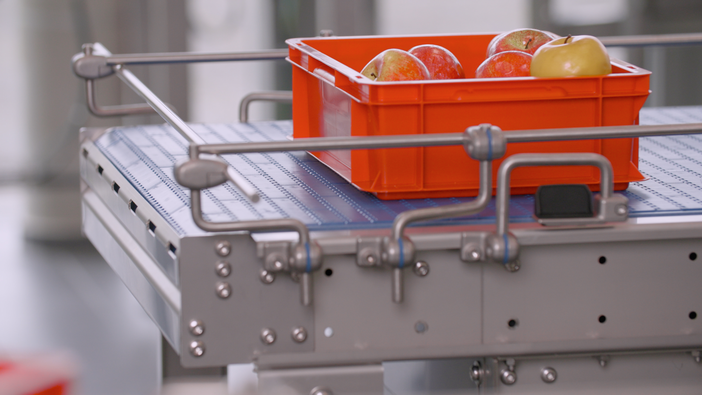